HOME > Production System > Overview of the gear grinding technology
Overview of the gear grinding technology
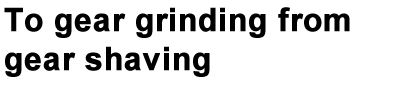
We abolished the shaving process in gear manufacturing and developed a processing technology to improve the gear accuracy as well as to remove the distortion after the heat treatment process in the tooth surface by newly adopting a grinding process by CBN electrodeposited worm-like grindstone with uniform truing.
This processing technology can finish a large number of gears with stable processing accuracy and correspond flexibly even for gears of high-mix and low-volume production. Also, this technology exerts an excellent effect on high accuracy and inexpensive manufacturing, by suppressing the cost to maximize of the tool.
This processing technology can finish a large number of gears with stable processing accuracy and correspond flexibly even for gears of high-mix and low-volume production. Also, this technology exerts an excellent effect on high accuracy and inexpensive manufacturing, by suppressing the cost to maximize of the tool.
What does the “RL” of 2RL tooth surface grinding mean?
Kikuta Iron Works original method which is based on the following three concepts; 2R for gRapidh and gReasonableh, L for gLong Lifeh
The core technology of RL tooth surface grinding
abrasive grains electrodeposited worm-like grindstone | ![]() |
In-house procurement:Designed and manufactured in-house (except the abrasive grains electrodeposition) |
To maintain accuracy:Shaping the CBN abrasive grains properly in special truing device. | ||
![]() |
Why is gear grinding cost cheaper by RL tooth surface grinding?
ƒTechnical point of view„EProcessing accuracy tends to be stable because the CBN abrasive grains exhaust extremely slower than the firing abrasive grains.
EWe uniformed the configuration state of each CBN abrasive grains in the grinding wheel by our own truing.
EThe number of shaping times of the abrasive grains is drastically reduced compared to the firing wheels.
EWe achieved high productivity grinding processing by tooth surface grinding machine in a modification of conventional hobbing machine.
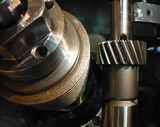
ƒEconomic point of view„
EInexpensive cost of the grinding wheels and dressing gears because of in-house procurement.
EInitial cost of equipment is inexpensive.
EReducing the tool cost by reproduction use of the grinding wheels.
ESuppressing the production cost by grinding processing corresponding to the automatic production line.
VA&VE proposal@`Recommendation of method substitution to RL tooth surface grinding processing from shaving processing`
We offer you high quality gears, with the production cost similar to shaving processing, and much cheaper than conventional gear grinding cost adopting the RL tooth surface grinding method.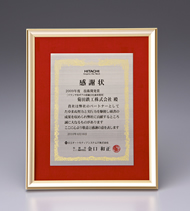
Technology Development Award (April 16, 2010)
by development of low-noise tooth of the balancer gear

by development of low-noise tooth of the balancer gear

Main specifications and application module of RL tooth surface grinding machine.
Maximum work diameter | 200mm | Vertical movement amount of spindle | 300mm |
Head turning angle of grinding wheel | ±35 degrees | Maximum spindle speed | 8000rpm |
Maximum table rotation speed | 500rpm | Application module | M0.8`2.0(2.5) |